Our Paint Line
Understanding our powder coating process
One of the key benefits of using AluK windows, doors and curtain walling is that they are virtually corrosion and maintenance free. That’s because the surface of the aluminium we use is pre-treated and then powder coated by us to ensure maximum durability, even in coastal and highly polluted environments.
Pre-treatment
Paint Technology
The large-scale vertical paint line at our Chepstow production facility has two separate spray booths which together give us a capacity of almost 700m2 of painted profile per hour.
We use only AkzoNobel Interpon powder coatings, which are specially designed for the architectural and construction industry and proven in use for the last 40 years. Like our pre-treatment, our powder coating process is approved by Qualicoat and GSB to offer an excellent combination or exterior durability and both colour and gloss retention.
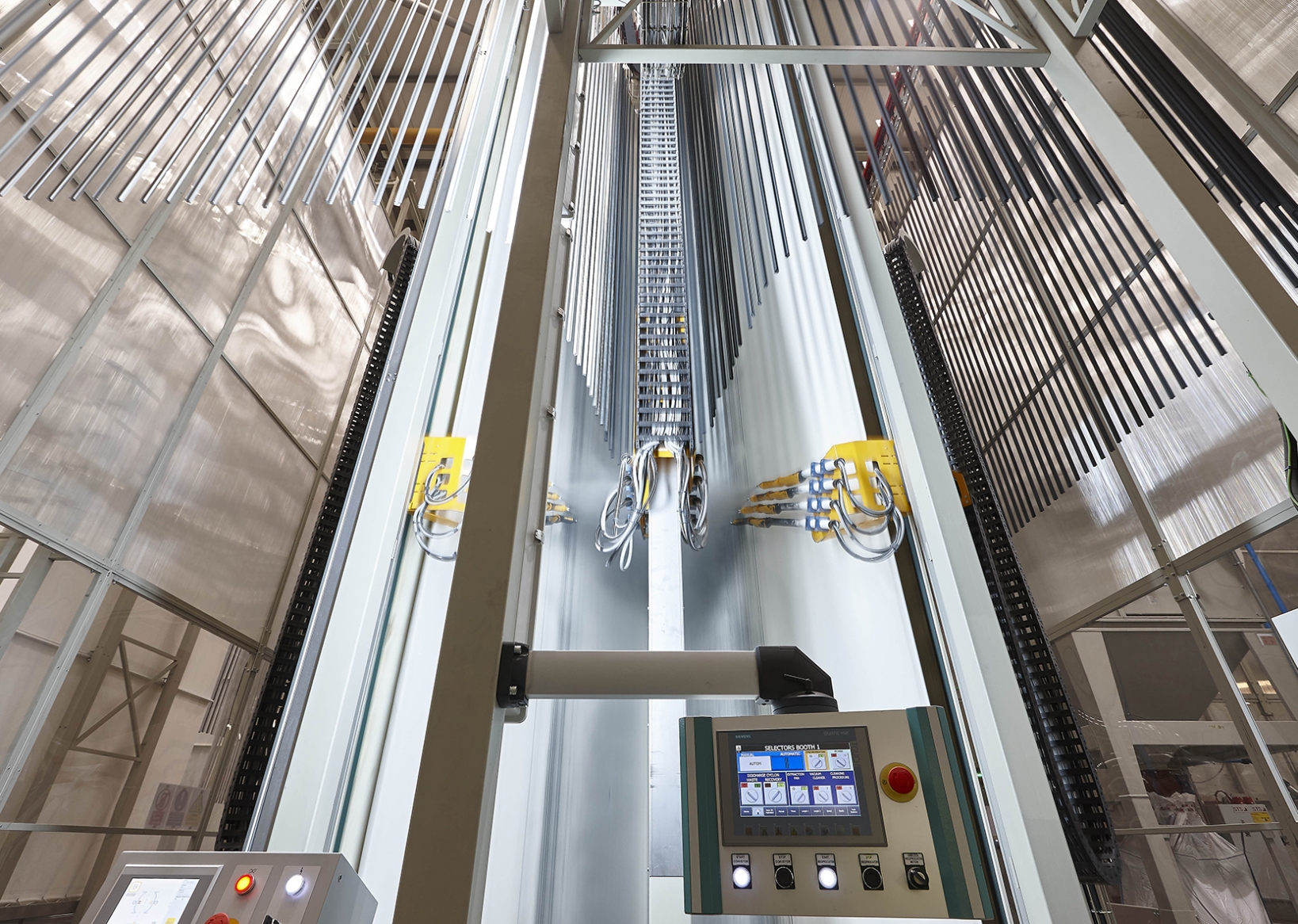
Qualicoat Approved
Customers can relax knowing that, by choosing a ‘Qualicoat approved’ product, both the pre-treatment and the powder coating are tightly controlled, and the finish provided meets specific parameters.
At AluK, we can supply to either Qualicoat Class 1 or Class 2 classifications, which relate to the weathering ability of the finish, the resistance to fading from UV light and the impact of temperature and humidity. These classifications are based on the globally accepted ‘Florida’ weathering test, which assesses long-term performance of panel samples exposed at a given 5° angle at certain pre-determined south facing locations in the US state. (Class 1 powders have achieved a ‘1 year Florida pass’ while Class 2 powders have achieved a ‘3 year Florida pass’.)
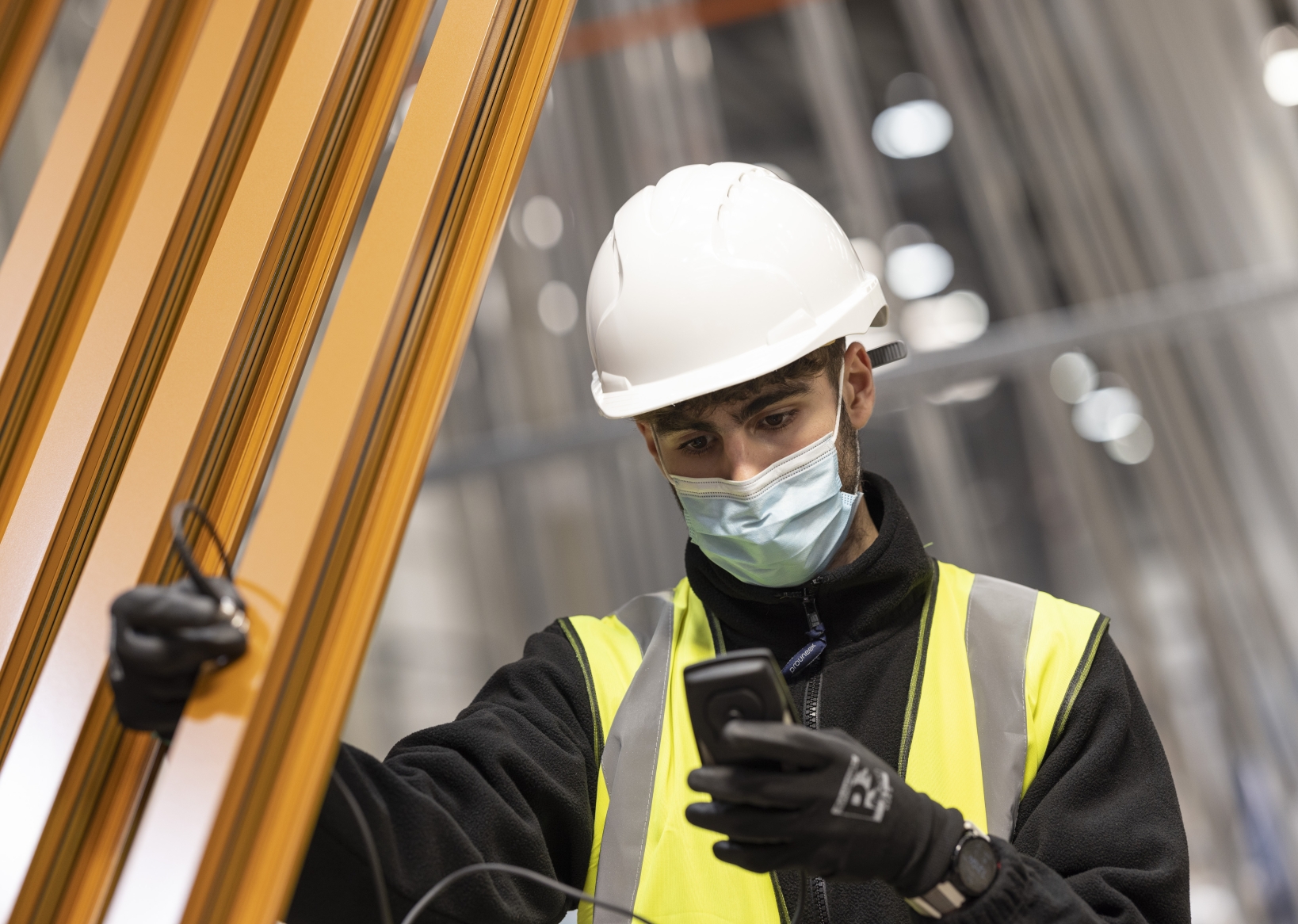
Because our paint line is one of the newest and most modern of any aluminium systems house, we are able to deliver the kinds of efficiencies and environmental impact reductions which are simply not possible using older technologies. For instance, we capture 98% of the excess powder used in our spray booth so that it can be filtered and reused to minimise waste. And, we also have our own effluent treatment plant where the water we use in treated and filtered. By the time we release it back into the environment, it is even cleaner than mains drinking water.
Our pre-treatment process is dual etching (Qualicoat Type AA1 - alkaline and acid) and 100% chromate free – relying on zirconium and titanium components instead. We use only Chemetall approved chemicals in our pre-treatment process including eco-friendly Gardobond® X4707 technology, which provides excellent corrosion protection for the aluminium substrate and an ideal surface for optimum paint adhesion. Gardobond® X4707 treated aluminium has been proven to match the filiform corrosion performance of chromated profiles and is approved by both Qualicoat and GSB. Using a cascade process with multi chemical and rinsing stages, we can deliver a coating weight of between 3 and 20 mg/m2 of both zirconium and titanium onto the aluminium. We also continually recycle and reuse the demineralised water used in the pre-treatment process so there minimal waste.